Better Industrial Defrosting with Tubular Heating
The Fascination with Electric Heating Applications
Electric heating elements play a crucial role in industrial de-icing and defrosting processes across various industries. Over the years, I've come across many different uses, including:
- Marine exhaust heaters for engine protection.
- Duct heating systems used for drying corn.
- Silicone rubber heaters to heat defibrillator batteries in emergency vehicles.
One fascinating use is in refrigeration heaters for preventing fog and ice on refrigerator doors. Industries like food and beverage, medical storage, and transportation need clear refrigerator doors for visibility and easy access.
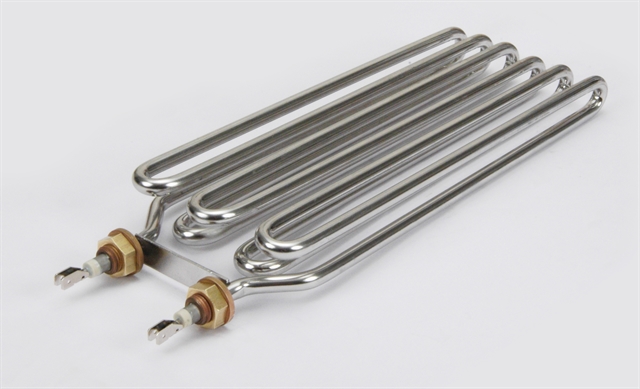
How the Traditional Defrosting Process Works
Most refrigeration systems use heat trace cables on the inner layer of the door frame to prevent fogging and ice. This method helps with thermal management by providing limited heat. This provides limited heat to keep the doors from fogging over or icing up because of constant opening and closing. You'll find this is standard practice across multiple industries with similar types of applications.
Tempco's Custom Tubular Heater Solution
Our client came to us to help create a better way to handle the defrosting process. Instead of lining the door frame with heat trace cable, they designed an airflow tunnel within the door frame. This applied forced heated air through this tunnel.
Tempco helped by creating a custom tubular heating element. This element fits within the space limits of the special airflow tunnel in the door frame. The heated air flows through the tunnel, providing more consistent heat to keep the door clear of fog and ice.
Benefits of the Improved Design
This new design offers several benefits over traditional methods:
- Lower Maintenance Costs: The tubular heater is more durable than heat trace cables, reducing the need for frequent repairs.
- Faster Defrosting: With a more consistent heat flow, doors defrost faster, ensuring minimal disruption.
- Easier to Replace: If the heater fails you can quickly and easily swap out the tubular element. Which is more efficient than the complex heat trace cable system.
Additional Benefits of Custom Heating Solutions
Beyond these advantages, custom tubular heating elements improve thermal management by providing precise control over the heating process. This means that the system wastes less energy and operates more efficiently, which leads to lower cost of operations. This is especially true for refrigeration systems that run continuously.
In addition, the custom nature of these solutions allows businesses to tailor the system to their specific needs. Custom designs offer flexibility for industrial de-icing, refrigeration defrosting, and heating sensitive electronic parts. This ensures businesses receive the most reliable and efficient system for their needs.
Electric heating elements are essential across industries for applications such as marine exhaust heaters and refrigeration defrosting systems. With custom solutions like tubular heating elements, companies can improve their industrial de-icing and defrosting processes, save on maintenance, and increase system reliability. No matter the industry, the right heating solution can make a difference in keeping systems running smoothly.
August 17, 2021
Please wait while we gather your results.
Related Articles
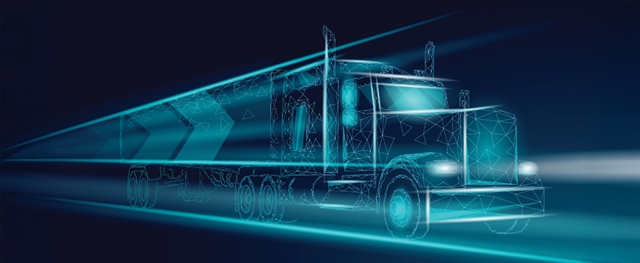
Did you know that a custom duct heater can maintain precise temperature control in wind tunnels with air speeds over 1,000 feet per minute? Learn how tailored HVAC solutions for wind tunnels are crucial for accurate aerospace, automotive, and vehicle testing!
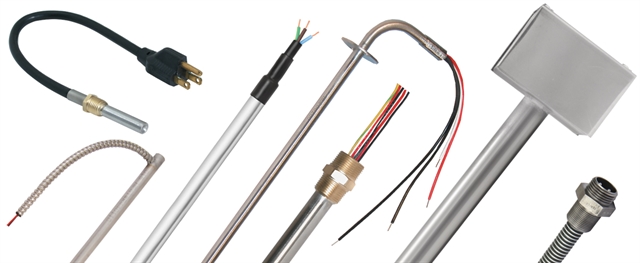
Explore the construction, uses and benefits of Tempco's cartridge heaters and discover how they can work for your industrial application.
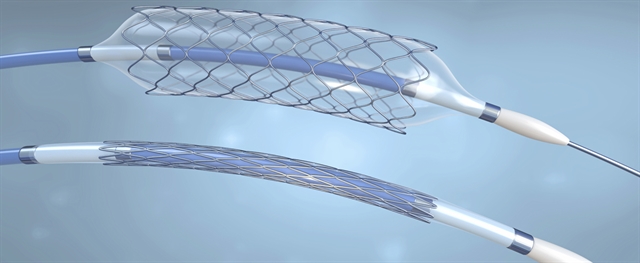
One OEM and medical device manufacturer specifies Tempco products for precise heating and accurate temperature sensing in their application.
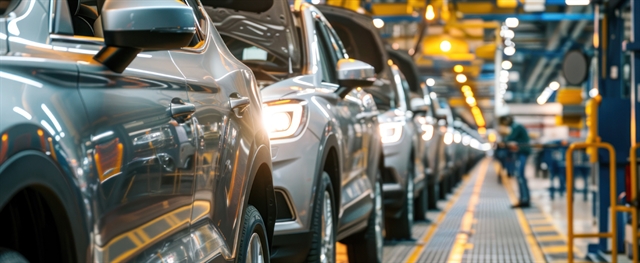
Tempco designed and manufactured a custom RTD with precise temperature control and measurement for our customer amid their supply chain challenges.